Wielandmotor
Der Wielandmotor, auch Blechwankel genannt, war ein aus geprägten Stahlblechteilen geschweißter und zusammengelöteter Kreiskolbenmotor. Er entstand Anfang der 1970er-Jahre bei der Audi AG in NSU nach den Ideen des Planungsleiters Werner Wieland. Der Motor lief auf dem Prüfstand und wurde im Ro 80 im Versuch gefahren.
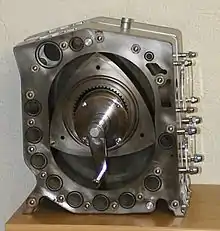
Aufbau
Der Motor ist einer der wenigen in der Geschichte der Motorenentwicklung und der einzige Wankelmotor, der aus Stahlblechteilen aufgebaut war. Diese Konstruktion brachte gegenüber dem im Gießverfahren gefertigten Wankelmotor Vorteile bei Gewicht, Kühlung, Laufruhe, Fertigungskosten und Langlebigkeit.
Im Zug der weltweiten Abwendung vom Wankelmotor (Ausnahmen: Mazda und experimentelle Flugzeugmotoren) kam der Wielandmotor nie zur Serienreife. Er bietet jedoch auch für die Zukunft Potential als Range-Extender für E-Autos: leicht, leise, kleine Bauweise, vibrationsarm und nochmals 22 % leichter als der gegossene Motor. Gewichtseinsparung bedeutet mehr Reichweite. Er ist darüber hinaus sehr gut als Wasserstoffmotor geeignet.
Die folgenden Patente erhielt die Konstruktion:
- Gehäuse für Kreiskolben-Brennkraftmaschinen in Trochoidenbauart und Verfahren zu seiner Herstellung.
- Mehreckiger Kolben für KKM
- Zwischenteil für KKM
- Dichtleisten speziell für Stahlblech-Ausführung – KKM.
Beim Aufbau ging man davon aus, die in einem Gießverfahren auftretenden Schwierigkeiten, wie einen möglichen Versatz der Gußkerne und den dadurch verursachten Ausschuss sowie Kernsandrückstände, die in den Kühlkreislauf gelangen können, zu vermeiden. Die besonderen und kostensenkenden Vorteile liegen in einer bedeutenden Verringerung des Gewichts bei 22 % und somit günstigerer Kühlung durch dünnere Wandungen sowie in einer Minderung der Herstell- und Fertigungskosten und beim Drehkolben zusätzlich in der unwuchtvermeidenden Gleichförmigkeit der Einzelteile.
Der vorgeschlagene Drehkolben besteht praktisch ausschließlich aus Blechteilen, nämlich unter sich gleichen, die Außenfläche bildenden segmentförmigen Kolbenflanken, an den Scheitelkanten eingefügten Einsatzstücken, zwei an ihrem Innendurchmesser zusammenstoßenden, flanschförmigen Ringen für die Kolbennabe mit -lager, auf der Kolbennabe im Bereich der Öldurchbrüche aufsitzenden Ölleitblechen, die Seitenteile durchstoßenden Druckausgleichsrohren sowie zwei dreieckigen Platten als Kolbenstirnwände, von denen eine das vorbearbeitete, gehärtete und nachgearbeitete Hohlrad enthält.
Die Außenkonturen der Kolbenstirnwände sind maßlich so genau hergestellt, dass sich hier wie an den Verbindungsstellen sämtlicher Einzelteile das Aufbringen von pastenförmigen Lötmitteln ermöglicht, das wahlweise auch galvanisch aufgetragen werden kann und in diesem Fall darüber hinaus einen zusätzlichen Oberflächenschutz bedeutet. Danach wurden die Einzelteile dicht und zunderfrei untereinander verbunden.
Der Gehäusemantel ist überwiegend aus Blechteilen hergestellt, und zwar aus einem die Umfangswand bildenden, mehrmals abgewinkelten und gebogenen Flacheisen, in dem die Öffnungen für Zündkerze, Ein- und Auslass sowie Kühlwasserumlauf bereits vorbearbeitet sind, aus der die Lauffläche bildenden Trochoide. Deren Form besteht aus zwei Flacheisen, die gleichförmig gezogen und verschweißt hergestellt werden, wobei die Wärmeableitung durch deren Wandstärke beeinflusst werden kann, ferner aus Verstärkungstruppen, die die Trochoiden gegen die Außenwand abstützen, aus mehreren, rohrförmigen Abstandsbuchsen, aus je einem Rohrstutzen für den Ein- und Auslass aus einem trichterförmigen Aufnahmestück für die Zündkerze, aus zwei gewölbten, in den Kühlraum eingelegten Wasserleitblechen sowie aus Bolzen für die Gewindesacklöcher der Anschraubteile und einem vorgebohrten Vierkantstück für die Vergaservorwärmeinrichtung. Die Seitenwände sind einschließlich der Bohrungen formgestanzt, wobei der innere Durchbruch die maßlich genaue äußere Kontur der Trochoide aufweist, sodass hier eine radiale Lötverbindung entsteht.
Das Zwischenteil besteht vorwiegend aus Blechteilen, und zwar aus einem die Umfangswand bildenden, mehrmals abgewinkelten und gebogenen Flacheisen, in das die Öffnungen für den Ölzu- und -ablauf bereits angearbeitet sind, aus mehreren rohrförmigen Abstandsbuchsen und axial angeordneten Kühlwasserdurchlaufrohren, aus vorgeformten, den Ölkreislauf trennenden Flacheisen, aus mehreren, zur Versteifung dienenden und den Kühlumlauf bestimmenden, kammförmigen Flacheisen sowie den formgestanzten Seitenwänden.
Der Heft- und Lötvorgang des Mantels und des Zwischenteils geschieht auf gleiche Weise wie beim Kolben. Die Herstellung der Seitenteile ist ebenfalls wie hier beschrieben.
Beim gegossenen Kreiskolbenmotor traten einige Probleme auf: Rattermarken, eingefallene Laufflächen schneller Verschleiß dadurch hoher Verbrauch. All diese Umstände bestärkten Werner Wieland umso mehr, den Drehkolben und die Gehäuseteile aus mehreren Stahlblechteilen herzustellen. Die Probleme des gegossenen KKM konnten beim Stahlblechmotor einfach und schnell gelöst werden.
Nach jedem Testlauf waren im nächsten Motor Änderungen möglich. Verstärkungen im heißen Bogen, andere Wasserleitbleche, neue Materialien und Härtemöglichkeiten, die in einem Arbeitsgang mit dem Löten möglich waren. Oft liefen im gleichen Motor mehrere Paarungen von Materialien gleichzeitig.
Die nicht befriedigenden Dichtleisten beim Wankelmotor veranlassten Werner Wieland, auch hier mit Patenten einzugreifen.
Das Ergebnis: Eine runde Welle in einem Trägerteil, die sich ähnlich wie in einem Rollenlager drehen konnte, löste auch dieses Problem.
Testergebnisse
Der gegossene KKM 871 hatte 2×750 cm³ Kammervolumen und leistete 170 PS. Der Verbrauch im Ro 80 bei 210 km/h lag bei 15,2 l/100 km Normalbenzin. Der Blechwankel mit der Versionsnummer KKM 871/1 hatte ebenfalls 2×750 cm³ Kammervolumen und leistete bei 6500/min 188 PS. Der Verbrauch verbesserte sich auf 12,7 l/100 km Normalbenzin.
Es wurden mindestens 250 Motoren gebaut und im Versuch und im Fuhrpark gefahren. Werner Wieland fuhr selbst lange Zeit einen RO 80 mit Blechwankel.
Literatur
- Gerhard Bauer: Über vierzig Jahre Wielandmotor, alles aus Blech oder was ? In: Wankel Journal, Heft 67 vom Juni 2013, S. 25–28 (online bei ro80club.org).
- Christian Gleichauf: Als Frechheit siegte. In: Heilbronner Stimme vom 10. September 2013 (online bei stimme.de).
Patente
- Werner Wieland: Built-up rotor construction for rotary mechanisms Patent Nr.US 3920358 A (google.com)
- Werner Wieland: Mehreckiger Kolben für Kreiskolbenbrennkraftmaschine und Verfahren zu seiner Herstellung DE 2355738 A1 (google.com)
- Werner Wieland: Housing for circular piston combustion engine of trochoid type and method of producing the same (patents.justia.com)