Robustness Validation
Robustheitsbewertung bzw. engl. robustness validation ist eine Qualifikationsstrategie, mit welcher die Robustheit eines Produkts gegenüber den Belastungsbedingungen einer realen Anwendung nachgewiesen wird und gezielt Aussagen über Risiken und Zuverlässigkeit getroffen werden können. Diese Strategie kommt besonders in der Automobilindustrie zur Anwendung.
Geschichte
Zu Beginn der 1970er Jahre waren noch vergleichsweise hohe Ausfallraten elektronischer Bauelemente in Automobilen tolerierbar, weil sie mechanische Komponenten ersetzten, die eine weit höhere Ausfallrate aufwiesen. Die zugrundeliegenden Ausfallraten von Bimetall-Blinkgebern lagen bei 10 % pro Jahr und die Lebensdauer von mechanischen Zündkontakten bei 10.000 km. Mit der steigenden Anzahl von Halbleitern in den Steuergeräten und durch die Einführung der ersten Sicherheitssysteme (ABS) entstand in den 70er Jahren zusätzlicher Handlungsbedarf. Bereits 1975 wurde die General Specification for IC´s in Automotive Applications[1] als erste SAE Recommendation herausgegeben, die 1978 zum SAE Standard[2] deklariert und von den wesentlichen Halbleiter-Herstellern übernommen wurde.
Die Gründung des Automotive Electronic Councils (AEC) 1994 durch Ford, Chrysler, GM-Delco war gleichzeitig der Startpunkt für das AEC Q100-Qualifikationsverfahren[3] auf Basis des SAE-Standards.
Gekennzeichnet ist dieses Verfahren durch unspezifische Tests, die ein breites Spektrum von möglichen Fehlermechanismen abdecken sollen, jedoch lediglich über Funktionalität des Bauteiles entscheiden. Aufgrund der Weiterentwicklung der Automobilelektronik und der ständig wachsenden Komplexität in den Fahrzeugen verbunden mit den Forderungen nach geringeren Fehlerraten ist dieses Qualifikationsverfahren nicht mehr zeitgemäß. Um Aussagen über die Robustheit treffen zu können, soll AEC Q100 durch Robustness Validation abgelöst werden.
Initiatoren und Mitwirkende
Im April 2007 wurde das Handbook for Robustness Validation of Semiconductor Devices in Automotive Applications[4] unter internationaler Zusammenarbeit vom SAE, ZVEI, AEC und JSAE (Japanese Society of Automotive Engineers) veröffentlicht, in welchem die Leitlinien für die zeitgemäße Validierung von Halbleiterkomponenten im für den Einsatz im Automobil zusammengestellt sind. Mitgewirkt haben hierbei Firmen aus der gesamten Lieferkette im Bereich der Automobilelektronik. Neben Fahrzeugherstellern und Zulieferern hat eine große Gruppe von Halbleiterherstellern dieses Qualifikationskonzept mit einer aktuellen Datenbank ergänzt. Diese sogenannte Knowledgematrix[5] beinhaltet eine Aufstellung aktuell bekannter Fehlermechanismen mit Ursachen, Fehlermethoden und weiteren Angaben.
Inhalt
Robustness Validation soll die Zuverlässigkeit von elektronischen Komponenten bewerten, indem die konkreten Anforderungen an das Produkt mit den tatsächlichen „Lebenswerten“ verglichen werden. Mit der Einführung dieser Methodik wird eine konkrete Aufstellung der Anforderungen (meist ausgehend von den OEMs) notwendig. Die Anforderungen an das Produkt werden unterschieden in die Umweltanforderungen (Mission Profile) und die funktionalen Anforderungen (Use-Cases).
Mission Profile
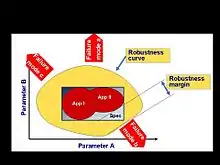
Das Mission Profile beschreibt die Belastungen und Beanspruchungen, welche auf das Produkt im realen Einsatz wirken. Dies sind zum Beispiel Temperaturwechsel, Temperaturprofil, Vibration und das Wirken von elektrischen und magnetischen Feldern oder auch anderen Umwelteinflüssen. Es gilt, die relevanten Stressoren in ihrer Art, Intensität und Einwirkungsdauer, sowie den Mix so genau wie möglich anzugeben. Mit diesen Angaben sind dann im Rahmen vorgegebener Genauigkeit Projektionen in Bezug auf Zuverlässigkeit der Applikation und ihrer Komponenten im Feldeinsatz möglich.
Use-Cases
Die Use-Cases beschreiben die Art und die Häufigkeit der Betriebszustände, für die das Produkt ausgelegt ist. Aufzuführen sind hierbei außer dem Normalbetrieb auch die möglichen Fälle von Sonderbetrieb und Notlauf. Hiervon abzugrenzen ist der nicht zulässige, wissentliche Missbrauch.
Robustness Margin
Die abgesicherten Lebensdauern werden durch spezielle, auf den Anwendungsfall und den Fehlermechanismus zugeschnittene, Tests ermittelt. Ein wesentliches Verfahren sind End of life tests. Aus dem Abstand der Anforderungen zu den Testergebnissen kann die Zuverlässigkeit sowie die Robustheit des Bauelementes bestimmt werden.
Produktentwicklung
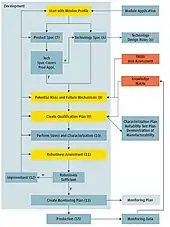
Die heute üblichen Qualifikationsverfahren für elektronische Bauelemente, Baugruppen und Komponenten im Automobilsektor beruhen auf der Anwendung von standardisierten Tests zum Ende der Produktentstehung der Bauelemente und Komponenten. Im Gegensatz dazu ist Robustness Validation ein Prozess, der den gesamten Produktentstehungsprozess, sowie die Serienfertigung einschließt. Die Qualifikation der Komponenten auf Basis der Robustheitsbewertung erfolgt somit implizit. Mit der Einführung von Robustness Validation werden Schwerpunkte im Entwicklungsprozess neu definiert. Ziel ist es, die Fehlerentstehung während der späteren Projektphasen zu reduzieren, wobei mittels Frontloading Maßnahmen zeitiger im Produktentstehungsprozess durchgeführt werden müssen.
Notwendig ist es, die Anforderungen vom Produkt auf die nächste Stufe der Wertschöpfungskette herunterzubrechen, um gezielt Aussagen zu möglichen Schwachstellen treffen zu können. Bereits in den frühen Projektphasen wird auf das Wissen (z. B. aus Wissensdatenbanken, Lessons Learned) vorangegangener Projekte zurückgegriffen, um dokumentierte bekannte Schwachstellen zu vermeiden. Mithilfe der Analyse der Änderungen des neuen Produktes und der Anwendung verschiedener Methoden, wie zum Beispiel FMEA, DRBFM oder Design Reviews können neue potenzielle Schwachstellen erkannt werden, um mögliche auftretende Risiken frühzeitig zu analysieren und zu vermeiden. Die hiermit aufgestellten kritischen Parameter werden zur Analyse der Durchführbarkeit des Projektes verwendet und fließen gegebenenfalls mit in die Änderung der anfangs aufgestellten Produktanforderungen mit ein. In der Validierung findet der Nachweis über die funktionale Machbarkeit und die Zuverlässigkeit statt, wobei die funktionale Erfüllung und die Umsetzung des Pflichtenheftes geprüft werden.
Weitere Anwendungsfelder der Robustness Validation
Neben der Veröffentlichung des Handbuches zur Robustness Validation für Halbleiterbauelemente im Jahre 2007 wurde im ZVEI im Jahre 2008 ein weiteres Handbuch[6] veröffentlicht, in dem diese Vorgehensweise für die Entwicklung und Qualifizierung von elektronischen Steuergeräten im Automobil beschrieben ist. Weitere Aktivitäten gibt es im Bereich der Sensoren sowie für elektronische Systeme im Fahrzeug.
Weblinks
- Homepage ZVEI
- Robustness Validation (ZVEI Internet)
- SAE J1879 Robustness Validation Standard
- Homepage Automotive Electronics Council
- siehe auch: Entwurf Robuster Nanoelektronischer Systeme
- siehe auch: Robuster Entwurf von neuen Elektronikkomponenten für Anwendungen im Bereich Elektromobilität (RESCAR)
Einzelnachweise
- General Specification for IC´s in Automotive Applications, SAE Recommondation, 1975
- General Specification for IC´s in Automotive Applications, SAE Standard, 1978
- Automotive Electronic Council’s Stress Test Qualification for Integrated Circuits, AEC Q100, Rev. G, 2007, auf aecouncil.com
- Handbook for Robustness Validation of Semiconductor Devices in Automotive Applications ZVEI, 04/2007
- Knowledgematrix bei zvei.org (MS Excel; 73 kB)
- Handbook for Robustness Validation of Automotive Electric/electronic Modules, ZVEI, 04/2008