Produzieren im Takt
Produzieren im Takt (PIT) ist eine Methode zur Auftragserzeugung, Auftragsfreigabe und Kapazitätssteuerung im Rahmen der Produktionsplanung und -steuerung.[1][2] Sie zielt in hohem Maße auf die Optimierung der Termintreue durch Schaffung eines konstanten Produktionsflusses. Sie unterscheidet sich gerade in der Abarbeitungslogik erheblich von bekannten Planungs- und Steuerungsmethoden. Ihr Einsatzgebiet sind komplexe Produktionen mit multidirektionalem Materialfluss und hoher Variantenvielfalt.
Im Vergleich zu vielen anderen Methoden setzt sie dabei bewusst auf eine Vergröberung der Planung (hier im Besonderen die Terminplanung), um sowohl eine Vereinfachung als auch eine Aufwandsreduktion der Planung und Steuerung zu erreichen. Sie wurde in ihren Grundzügen von Löllmann und Färber[3][4] entwickelt.
Funktionslogik von PIT
Abbildung 1 visualisiert die Funktionslogik von PIT. Jede Ressource wird durch einen Plantopf mit einer spezifischen Taktdauer repräsentiert. Hinter einer Ressource können sich sowohl eine als auch mehrere, sinnvoll zu aggregierende Kapazitätseinheiten verbergen.
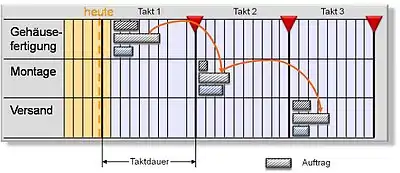
Im Rahmen der Durchlaufterminierung vergibt der Planungslauf des PPS-Systems in Abhängigkeit von Plantopfkapazität und Taktdauer mehreren Aufträgen identische Start- und Endtermine je Ressource. Dies hat zur Folge, dass jeweils zu Beginn eines Taktes an jeder Ressource mehrere Aufträge zur Bearbeitung zur Verfügung stehen, von denen jeder ausgewählt werden darf, ohne die Termine der eingeplanten Aufträge zur gefährden. Die Zeit zwischen Start- und Endtermin eines Topfs wird als Taktdauer bezeichnet.
Nach Ablauf des Taktes wandert der Arbeitsinhalt eines jeden Taktes zur nächsten Ressource weiter. Nun stehen auch hier wieder in Abhängigkeit vom Materialfluss mehrere Aufträge zur Bearbeitung an. Diese Logik wiederholt sich nach Ablauf jedes Taktes. Die Taktdauern der einzelnen Ressourcen können voneinander abweichen. Sie sollten jedoch ganzzahlige Vielfache voneinander darstellen, um Aufträge, die nicht in einem zur Bearbeitung bereitstehenden Takt liegen, zu vermeiden.
Auftragserzeugung
Durchlaufterminierung
Die Durchlaufterminierung erfolgt primär als Rückwärtsterminierung, bei der ausgehend vom Kundenwunschtermin jeder Arbeitsvorgang eines Auftrags in den Topf der für die Bearbeitung erforderlichen Ressourcen eingeplant wird. Dies findet so lange für alle Aufträge mit ähnlichem Kundenwunschtermin statt bis die Kapazität einzelner Ressourcen im Auftragsdurchlauf erschöpft ist. Dann erfolgt eine Verschiebung der nachfolgenden Aufträge in die Zukunft bis der Engpasstakt wieder freie Kapazität besitzt. Alle Arbeitsgänge in einem Takt erhalten gleiche Start- und Endtermine. Folglich ergibt sich die arbeitsgangspezifische Durchlaufzeit jeweils aus der Taktdauer einer jeden Ressource, die auftragsspezifische Durchlaufzeit hingegen aus der Summe aller Taktdauern einer jeden für die Auftragsbearbeitung erforderlichen Ressource. Durch die Vergröberung des Termingefüges resultiert aus diesem Vorgehen eine sehr einfache und effiziente Kapazitätsplanung.
Kapazitätsplanung
Die Kapazitätsplanung im Rahmen der Terminierung erfolgt nicht, wie in bekannten Methoden gegen starre Kapazität, sondern gegen teilweise flexible Kapazitäten. Diese flexiblen Kapazitäten werden durch eine Kapazitätsauslastungsampel wie in Abbildung 2 je Ressource repräsentiert. Solange sich die Ampel auf der grünen Stelle befindet, ist eine Einplanung eines jeden Auftrags ohne weitergehende Abstimmung immer möglich. Der grüne Bereich der Ampel impliziert die Normalkapazität der betrachteten Ressource.
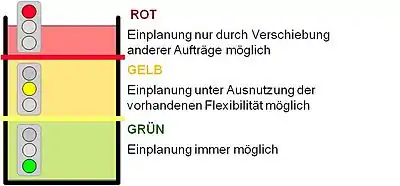
Befindet sich hingegen die Ampel im gelben Bereich, erfordert eine Einplanung eine Abstimmung des Planers mit der Produktion. Der gelbe Bereich deutet auf die Einplanung in einem definierten Flexibilitätskorridor einzelner Ressourcen hin. Beispielsweise können hierzu Kapazitäten kurzfristig aus anderen, aktuell geringer ausgelasteten Bereichen abgezogen oder Kapazitäten durch Springer o. Ä. mobilisiert werden. Dies hat den Vorteil, dass es keiner Änderung des Schichtmodells im verwendeten Planungssystem bedarf.
Eine Einplanung in den roten Bereich hingegen ist nicht möglich, da hier die Kapazitätsreserven der Produktionsressource überschritten werden.
Auftragsfreigabe
Die Auftragsfreigabe kann als Auftragsfreigabe nach Termin charakterisiert werden. Sie erfolgt für alle Ressource zyklisch nach Ablauf jedes Takts. Da sie nicht ereignisorientiert stattfindet, reduziert dies den Aufwand erheblich. Nicht jeder einzelne Auftrag oder Arbeitsgang muss verfolgt und freigegeben werden, sondern stets ganze Auftragsbündel mit identischen Start- und Endterminen.
Kapazitätssteuerung
Die Kapazitätssteuerung kann in Abhängigkeit vom Umfang des Rückstands auf mehrere Arten erfolgen, wobei diese sich durch den von ihnen induzierten Aufwand unterscheiden.
Bei kleinen Rückständen erfolgt eine Abstimmung zwischen den Verantwortlichen der betrachteten Ressource und denen der Nachfolger. Es ist zu klären, ob der Rückstand in den Folgeperioden ohne negative Konsequenzen für das folgende Produktionsprogramm aufgeholt werden kann. Im positiven Falle kann eine aufwändige Umplanung und Rückführung des Rückstands in die Planung vermieden werden.
Bei größeren Rückständen ist zu überprüfen, ob nach Beendigung des Taktes Kapazitäten zum Abbau des Rückstands mobilisiert werden können. So kann beispielsweise im Einschichtbetrieb bei Takten mit der Dauer von einer Schicht direkt in der Folgeschicht der Rückstand abgearbeitet werden. Hier ist in Abhängigkeit von den betrieblichen Vereinbarungen zur Mobilisierung von Überstunden oder Wochenendarbeit sowie der aktuellen Auslastungssituation zu überprüfen, ob dies möglich ist.
Sollte sich dies als nicht realisierbar oder der Rückstand als zu groß für die genannten Maßnahmen erweisen, ist eine Umplanung der aktuellen Planungsergebnisse erforderlich.
Abarbeitungslogik
Aufgrund der Terminierungslogik mit identischen ressourcenspezifischen Eckterminen für mehrere Aufträge bzw. Arbeitsgänge können alle Aufträge bzw. Arbeitsgänge mit gleichen Terminen nach beliebiger Reihenfolge abgearbeitet werden. Somit hat die Logik den Vorteil, dass die bearbeitenden Personen beispielsweise in Abhängigkeit von erforderlichen Rüstrestriktionen deren Reihenfolge ohne Gefährdung der Terminsituation selbst bestimmen können. Dies fördert die Akzeptanz des Produktionsplans in der Ausführungsebene erheblich.
Unterschiede zwischen Produzieren im Takt und der normalen Durchlaufterminierung
- Es entstehen deutlich weniger Ecktermine als bei der normalen Durchlaufterminierung.
- Der Planungs- und Steuerungsaufwand wird durch die sinkende Anzahl zu koordinierender Termine erheblich reduziert.
- Alle sich in einem Takt befindenden Aufträge können nach beliebiger Reihenfolge abgearbeitet werden.
- Durch die in beliebiger Reihenfolge abzuarbeitenden Aufträge erfolgt eine Entkopplung der Aufträge zwischen den Ressourcen. Dies fördert die Robustheit der Planung gegenüber Terminverschiebungen.
Einzelnachweise
- H. Lödding: Verfahren der Fertigungssteuerung. Springer-Verlag, Berlin 2005.
- Günther Schuh (Hrsg.): Produktionsplanung und -steuerung: „Grundlagen, Gestaltung und Konzepte“ 3. Auflage. Springer-Verlag, Berlin 2006.
- http://www.lfconsult.de/files/upload/ARTIKEL/Artikel%20Wt-online.pdf (PDF; 393 kB)
- Ulrich Färber, Pit Löllmann: PIT-Ansatz - PIT Produzieren im Takt. In: www.lfconsult.de. LF CONSULT GmbH, 1. Januar 2017, abgerufen am 23. Januar 2017.