Metall-Katalysator
Metall-Katalysatoren bestehen aus einem Stahlträger (Monolithen) sowie der katalytischen Beschichtung. Neben den Keramik-Katalysatoren stellen die Metall-Katalysatoren in vielen Industriebranchen eine Alternative dar. Neben dem Einsatz als Fahrzeugkatalysator werden die Metall-Katalysatoren in Kleinmotoren wie in Kettensägen und Rasenmähern sowie in Industrieanlagen (Blockheizkraftwerke, Dieselgeneratoren etc.) eingesetzt.

Dieser Artikel wurde auf der Qualitätssicherungsseite des Portals Transport und Verkehr eingetragen.
Bitte hilf mit, ihn zu verbessern, und beteilige dich an der Diskussion. (+)
Die ersten Metall-Katalysatoren wurden Jahrzehnte vor Entwicklung und Einsatz der Keramik-Katalysatoren erfunden.
Aufbau
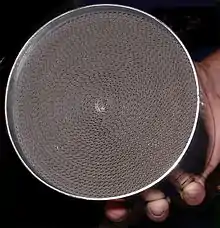
Metall-Katalysatoren bestehen in der Regel aus spiralförmig gewickelten, dünnen Metallfolien (meist aus abwechselnden glatten und gewellten Lagen) oder aus geschichteten Platten. Die heutzutage hauchdünn ausgewalzten Bleche (mit Dicken meist kleiner als 50 µm) bestehen aus hochlegierten Spezial-Edelstählen mit einem relativ hohen Aluminiumanteil (bis zu 10 %). Häufig wird dabei sogar von "Alu-Stahl" gesprochen. Aufgrund des hohen Aluminiumanteils, der für das Aufbringen der Washcoat sowie der Edelmetallschicht unabdingbar ist, lassen sich die Metall-Folien nicht miteinander verschweißen. In einem speziellen Verfahren werden die Kontaktpunkte (die Folienlagen unter sich und diese wiederum mit dem Metallmantel) daher im Hochvakuumofen hartgelötet, so dass eine hohe mechanische Festigkeit und eine präzise Zellenstruktur erreicht werden. Das Hartlöten verhindert zudem das gefürchtete "Ausspiralisieren" vor allem unter Last, also im täglichen Fahrzeugeinsatz.
Nach dem Vakuumhartlöten werden die Metall-Katalysatoren von den sogenannten Beschichtern mit der Washcoat und den Edelmetallen beschichtet. Danach werden sie an die Fahrzeughersteller oder andere OEMs verschickt.
Vorteile
Einer der wesentlichen Vorteile eines Metall-Katalysators ist seine geringe Zellwandstärke. Aktuell sind Metall-Monolithen mit Foliendicken von nur 20 µm im Einsatz. Zum Vergleich, die dünnsten Keramik-Monolithe weisen Wandstärken von 40 µm auf. Geringe Zellwandstärken bieten ein besonders günstiges Verhältnis von offenem Anströmquerschnitt zur geometrischen Oberfläche, dadurch verringern sie den Abgas-Gegendruck und einen möglichen Leistungsverlust. Immerhin betrug dieser bei den ersten (Keramik-)Katalysatoren noch 10 %.
Einen weiteren großen Vorteil stellt die niedrigere Wärmekapazität dar. Damit springen Metall-Katalysatoren sehr viel schneller an und können daher die Abgas-Schadstoffe rascher in die nicht giftigen Gase umwandeln. Eine hohe thermische sowie mechanische Stabilität selbst bei starken Temperatur- und Lastwechseln (Temperaturschocks), sind weitere Vorteile der Metall-Katalysatoren. Darüber hinaus besteht eine besonders flexible Gestaltung des Katalysatorquerschnitts. So gelangen runde, ovale (auch Racetrackformen), quadratische, sechseckige (etc.) zum Einsatz.
Da die Metallträger direkt in die Abgasanlagen verschweißt werden können, reduziert sich der Montageaufwand im Vergleich zu keramischen Substraten erheblich. Nicht zuletzt sind Fasermatten, die zur Lagerung der Keramik-Monolithe unverzichtbar sind, nicht notwendig. Immerhin gelten diese Fasermatten aus Aluminiumsilikat (nach wie vor über 90 % im Einsatz) gemäß EU-Einstufung als krebserzeugend.
Die Vollmetallkonstruktion der Metall-Katalysatoren verbessert zudem deren Recyclingeigenschaft.
Die am Markt derzeit noch aktiven Hersteller von Metall-Träger-/Katalysatoren sind die Firmen Ecocat / Vihtavuori / Finnland, Emitec in Lohmar, Oberland Mangold / Eschenlohe/Bayern, Emission Partner / Niedersachsen[1] sowie die Firma Lindo Gobex, Gorzów/Polen. Als Erstzulieferer für die Automobil- und Nutzfahrzeughersteller ist davon lediglich Emitec aktiv.
Als einer der größten Hersteller von Metall-Trägern (die eigentliche katalytische Beschichtung nehmen andere Zulieferer vor) hat sich das Unternehmen Emitec in letzter Zeit vor allem auf Metall-Monolithe mit Turbulenz erzeugenden Profilen spezialisiert. Diese mit longitudinalen und/oder transversalen Profilen / Durchbrüchen oder mit perforierten (gelochten) Metallfolien versehenen Metall-Katalysatoren sind bis zu 30 % leistungsfähiger als vergleichbare Keramik-Katalysatoren. Die strukturierten Kanäle brechen die laminare Strömung auf und sorgen für Turbulenzen. Diese wiederum erhöhen den Stoffaustausch zwischen den giftigen Abgasmolekülen und den katalytisch aktiven Komponenten an der Katalysatorwand und steigern letztendlich die katalytische Aktivität. Aufgrund der Turbulenz erzeugenden, strukturierten Metallfolien, lassen sich bei gleicher Reinigungsleistung um 30 % kleinere Katalysatoren herstellen. Damit können auch um 30 % der teuren Edelmetalle eingespart werden.
Die vielen Vorteile der Metall-Katalysatoren sorgten für deren umfassenden Einsatz vor allem bei Fahrzeugen mit motornahen Katalysator-Anordnungen. So wurden erstmals alle BMW 3er der Baureihe E46 mit Ottomotor mit motornahen Metall-Katalysatoren bestückt.
S- und SM-Form
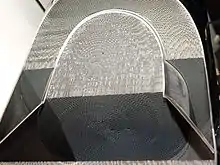
Im Fahrbetrieb ist der beschichtete Metallträger extremen Temperaturschwankungen, Schwingungen und Schlägen ausgesetzt. Er dehnt sich bei Erwärmung aus und schrumpft bei Abkühlung. Von einem bestimmten Durchmesser des Pakets an löste sich immer wieder die zweite Wickellage am Mantelumfang von der ersten und zerriss sie. Der daraufhin vorgenommenen sehr stabilen Lötverbindung waren wiederum die Folien selbst nicht gewachsen. Auch eine Vielzahl immer neuer Ideen zur Herstellung dehnungsfähiger Strukturen schlug regelmäßig fehl. Es galt also die Belastungen über den ganzen Trägerquerschnitt zu verteilen.
Parallel zur Entwicklung geeigneter Stahlfolienrezepturen liefen zahlreiche Hartlötversuche sowie die Entwicklung einer Qualitäts-Prüfmethode der gelöteten Träger in kaltem Zustand. Auch das Lötverfahren wurde in kleinen Schritten weiterentwickelt, bis man das ganze Hartlötverfahren mittels Vakuumtechnik beherrschte. Dabei gewann man die Erkenntnis, dass auch die Wickeltechnik der Folien entscheidenden Einfluss auf die Haltbarkeit der Lötverbindung hatte.
Das Problem der Dauerhaltbarkeit beim Metall-Träger wurde gelöst, indem statt einer einfachen Spiralwicklung eine S-förmige Wicklung verwendet wurde. Diese wurde von Emitec 1985 zum Patent angemeldet. Bei dieser Anordnung liegt nun nicht mehr Lage auf Lage parallel zur Gehäusewand, sondern nur noch die Enden der Einzelschichten kommen mit ihr in Berührung und werden mit ihr hartgelötet. Diese Bauweise ergibt einen Träger großer Stabilität bei zugleich hoher Elastizität, welche für die Wärmedehnung absolut notwendig ist. Aus anfänglich zwei Wickeldornen (für eine S-Wicklung) wurden im Lauf der Jahre drei Dorne (für eine M-Wicklung). Darüber hinaus sind auch vier Dorne und mehr möglich, wenn Träger mit großen Durchmessern etwa für Nutzfahrzeuge oder Stationärmotoren hergestellt werden sollen.
Ausführungen und Einsatzbereiche
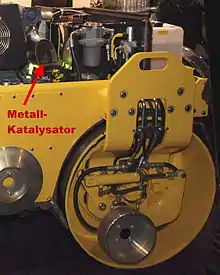
Die Leistungsfähigkeit der Katalysatoren wird durch die Art der Beschichtung, durch die Zelldichte cpsi (Zahl der Zellen pro Quadratinch von 150 bis 2.400 cpsi sind möglich) und durch das zur Verfügung gestellte Trägervolumen bestimmt. Es können produktionstechnisch Trägerdurchmesser von 28 bis 1.200 mm realisiert werden. Bei ganz großen Trägerdurchmessern haben sich in der Praxis allerdings einzelne, hexagonale Katalysatoren, die als Matrix zusammengesetzt werden können, vielfach durchgesetzt.
Metall-Katalysatoren finden in vielen Einsatzgebieten ihre Anwendung wie in Fahrzeugen (PKW, LKW, Motorräder, Non-Road-Fahrzeugen wie Baumaschinen, Flurförderzeuge wie Gabelstapler sowie Landmaschinen unter anderem in Traktoren, Eisenbahn-Lokomotiven sowie in Schiffen). Darüber hinaus gelangen sie in Kleinmotoren (z. B. Kettensägen, Rasenmäher) und in Industrieanlagen (Konventionelle Kraftwerke, Blockheizkraftwerken (BHKW) mit Dieselmotoren oder Gasturbinen oder stationäre Stromgeneratoren etc.) zum Einsatz.
Arten
Otto- und Dieselmotoren
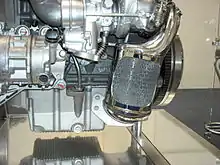
Metall-Katalysatoren gibt es als Drei-Wege-Katalysator für Ottomotoren und als Oxydationskatalysator für Dieselmotoren.
2004 setzte der Nutzfahrzeughersteller MAN nach langjährigen Versuchen erstmals den neu entwickelten Dieselpartikelfilter (DPF) vom Typ PM-(Particulate Matter-) Metalit, den PM-Kat, weltweit bei den Nutzfahrzeugmotoren der Baureihe D20 serienmäßig ein. Bei den Automobilen setzte als erster BMW den PM-Metalit im 1er Diesel-PKW ein. Später kamen Einsätze in der Serienfertigung der Diesel-Smart hinzu. Neben der Reduktion der Partikelmasse um mehr als 30 % wird vor allem die Anzahl der als besonders gesundheitsschädlichen Ultrafeinpartikel (Durchmesser kleiner 400 nm) um etwa 80 % reduziert.
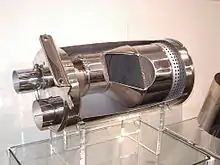
Da der Gesetzgeber bis heute keinen Unterschied zwischen groben Partikeln, die für die Partikelmasse zuständig sind und den gesundheitsschädlichen Feinstpartikeln macht, hat sich der Metall-Dieselpartikelfilter als Nebenstromfilter im Vergleich zum wanddurchströmten Keramikfilter im Automobilsektor bisher nicht durchgesetzt.
Ganz anders sieht es im Nutzfahrzeugbereich und vor allem bei Non-Road-Fahrzeugen aus. Aufgrund ihrer hohen Robustheit dominieren dort die Metall-Dieselpartikelfilter beziehungsweise die SCR-Systeme (SCR = Selective Catalytic Reduction), welche wesentlich auf den Konstruktionen des Metall-Dieselpartikelfilters aufbauen.
Zweirad-Metall-Katalysatoren
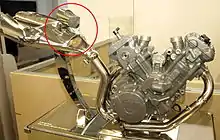
Bereits 1987 wurden Metallträger für Zweiradkatalysatoren (Viertakt- und Zweitaktmotoren) entwickelt und eingesetzt. Vor allem die aufstrebenden Schwellenländer China und Indien wollten die Emissionen ihres schnell wachsenden Zweirad- und Dreiradmarktes in den Griff bekommen.
In Indien beispielsweise werden hauptsächlich Metall-Katalysatoren für Zweitaktmotoren mit 125 Kubikzentimeter eingesetzt. Diese Motoren treiben vom Zweirad bis hin zu skurrilen dreirädrigen Transportvehikeln mit dem Namen "Tuk Tuk" eine Vielzahl an Fahrzeugen an. Die eingebauten Metall-Katalysatoren verhelfen den bisher stinkenden Motoren immerhin zu den Abgaswerten auf Niveau der Euro 2.
Heute werden auch Hochleistungsmotorräder wie Aprilia RSV4, BMW R 1200 sowie S 1000 RR oder KTM Super Duke ausschließlich mit Metall-Katalysatoren bestückt. Bruchempfindliche Keramik-Monolithen scheiden von vornherein aus.
Von Aprilia über Honda, Kawasaki bis hin zu Suzuki und Triumph setzen alle Motorradhersteller ausschließlich Metall-Katalysatoren ein. Selbst das urwüchsige Diesel-Motorrad Neander ist mit einem Metall-Partikelfilter bestückt. Hierbei handelt es sich übrigens um das erste Turbo-Diesel-Motorrad der Welt!
Industrie-Katalysatoren
Oberland-Mangold produziert nach eigenen Aussagen Metall-Träger bis 1.200 mm Durchmesser. Da diese großen und vor allem sehr schweren Einzel-Katalysatoren gewisse Probleme bei der Handhabung und Montage mit sich bringen, hat beispielsweise die Firma Emitec die HEXA-Kat-Module entwickelt. Hierbei handelt es sich um kompakte hexagonale, also sechseckige Metall-Träger (Breite an der schmalen Stelle entspricht der Schlüsselweite von 250 mm), die zu größeren Katalysatorpaketen zusammengefasst werden können. Damit lassen sich selbst größte Abgassysteme für Maschinen und Kraftwerke im MW-Bereich relativ einfach, flexibel und vor allem kostengünstig realisieren.
Geschichte
Der Metallträger als Basis für den Auto-Katalysator hat Generationen von Ingenieuren beschäftigt, lange bevor der Keramikträger als Lösung präsentiert wurde. Bereits 1929 erkannte Joseph Christie Whitney Frazer (* 30. Oktober 1875, † 28. Juli 1944) aus Baltimore/USA die Vorteile des Metallträgers und ließ im selben Jahr seine diesbezüglichen Entwicklungen patentieren. Das Patent beschreibt einen Katalysatorträger aus gewellter Stahlfolie, wobei die gewellten Folien durch glatte Folien voneinander getrennt wurden. Weitere Ansprüche nennen anstelle der gewellten Metallfolie Siebe oder Lochbleche. Das war keineswegs der erste Vorschlag für einen Abgaskatalysator, doch scheint Joseph Christie Whitney Frazer damit der Urvater des heutigen Stahlträgers für Metall-Katalysatoren gewesen zu sein. Frazer meldete seinen Stahlträger für Metall-Katalysatoren auch in Deutschland zum Patent an und erhielt 1930 das Deutsche Reichspatent Nr. 563757
Die Beschreibung sowohl des Stahlträgers wie des Katalysators aus Metalloxiden mutet außerordentlich modern an. Da die damaligen Motoren neben Kohlenmonoxid auch große Mengen unverbrannter Kohlenwasserstoffe (HC) enthielten, sah Frazer zusätzlich eine Sekundärlufteinblasung vor, die erst Jahrzehnte später im Automobilbau eingeführt wurde. Die Luftmenge, welche vor dem Katalysator eingeblasen werden sollte, wollte der Erfinder Frazer in Abhängigkeit von der Motordrehzahl regeln. Sehr frühzeitig erkannte Frazer auch, dass der Katalysator erst ab einer Abgastemperatur von 450 °C in der Lage ist, Kohlenmonoxid zu oxidieren. Darum empfahl er, das Abgas nach dem Kaltstart etwa durch ein elektrisches Heizgerät zu erwärmen. Erst Jahrzehnte später wurde der beheizte Katalysator Realität.
Mit dem beheizten Metall-Katalysator vom Typ EMICAT konnte erstmals der BMW Alpina B12 5,7 und kurz darauf das 12-Zylinder-Serienmodell der BMW AG die 1996 gültigen Emissionsgrenzwerte in Europa, Japan und USA deutlich unterschreiten.
Joseph C.W. Frazer weist mehrfach darauf hin, dass der Träger aus einem wärmeleitenden Metall bestehen müsse. Darum sei eine Berührung des Trägers mit der Wand des ihn umschließenden Behälters notwendig. Die im Träger entstehende Wärme wollte Frazer außerdem benutzen, um die zu kalten Abgase etwa im Leerlauf vorzuheizen. Die Beschreibung ist derartig detailliert, dass damals mit Sicherheit Versuche durchgeführt wurden. Siebartige Träger aus hochlegiertem Stahl hat es schon vor Frazer gegeben, offensichtlich stammen sie aus der Petrochemie. Somit gilt Frazer als Urvater der gelochten Metallträger.
Die Idee, Stahlträger für Autokatalysatoren zu verwenden, tauchte nach den Arbeiten von Frazer erst nach 1950 wieder auf, nachdem weitergehende Forderungen zur Senkung der Schadstoffe im Autoabgas immer stärker wurden. Einer der ersten Hersteller, der den Metallträger untersuchte, war UOP (Universal Oil Products) in den USA, welche später (1988) von Allied Signal und Union Carbide übernommen wurde. Auf Seiten der Automobilhersteller sind General Motors, Mercedes-Benz, Audi, VW und andere zu nennen. Alle scheiterten allerdings daran, dass die spiralförmig gewickelten Metallfolien lose in ihrem rohrförmigen Behältnis saßen und dem dynamischen Betrieb nicht gewachsen waren. Sie spiralisierten schnell und gingen dann rasch defekt.
Diese mechanisch harten Bedingungen sorgten wesentlich später bis in die Neuzeit für das Aus einer Vielzahl von Versuchen, von denen die meisten durch zahlreiche Patente bekannt wurden. Sie kamen von Ford, General Motors, Mitsui, der englischen Kernenergiebehörde, Degussa und anderen Unternehmen. Alle zeigten gewellte Metallfolien, einige auch die wechselweise Verwendung von glatten und gewellten Folien. Neben spiralförmig gewickelten Folien gab es jedoch auch Vorschläge, die Folien als Platten aufeinander zu legen und in rechteckigen Gehäusen unterzubringen. Mitsui ließ sich 1974 sogar eine Variante patentieren, bei der das Plattenpaket austauschbar war. Zudem fixierte man die Platten durch Schrauben, diese konnten einen Schwingungsdauerbruch dennoch nicht vermeiden. Aus leidvoller Erfahrung kannte man das Problem der losen Folienpackungen durchaus, aber eine endgültige Lösung stand noch aus.
Obwohl 1973 die ersten sogenannten Dreiwege-Katalysatoren mit Keramik-Monolith erfolgreich in den Markt eingeführt wurden, unterstützte die Automobilindustrie über Jahrzehnte hinweg alle Versuche, Stahlfolien als Träger zu verwenden. Neben den vielen Vorteilen der Metall-Katalysatoren wollte man sich von den damals zwei großen Keramik-Monolithherstellern (die Firmen Corning, USA und NGK, Japan; die japanische Denso kam erst viel später hinzu) unabhängiger machen.
Bei Audi, Ford, General Motors und VW beispielsweise liefen ab etwa 1960 zahlreiche Versuche, Metallträger bis in die Serie einzuführen. Bei Tests ließen sich damit ausgezeichnete Abgasreinigungsleistungen erzielen, doch war die Dauerhaltbarkeit dieser Metallträgerkatalysatoren nicht gegeben. Die spiralförmig gewickelten und dann lose eingesetzten Folien versuchte man zunächst durch kreuzförmige Halter an den Enden zu fixieren. In der Praxis, während des dynamischen Betriebs scheuerten diese kreuzförmigen Halter allerdings durch, so dass sich der Monolith (Träger) trotzdem ausspiralisierte. Das finnische Unternehmen Kemira (heute EcoCat) präsentiert 1985 einen Metall-Katalysator, der aus bereits mit Edelmetall beschichteten Folien bestand, die erst danach spiralförmig gewickelt wurden. Um ein Ausspiralisieren zu verhindern, wurde das gewickelte Folienpaket mittels nagelähnlichen Metallstiften am Mantel fixiert. Man sprach dabei auch vom „genagelten Metall-Katalysator“. 1987 baute Kemira in Vihtavuori, Laukaa, eine komplette Fertigungsanlage zur Herstellung dieser beschichteten Nagel-Metall-Katalysatoren. 1990 wurde die Serienfertigung aufgenommen und 1992 wurde beispielsweise das Opel-Modell Corsa mit diesem Nagel-Metall-Katalysator ausgerüstet. Neben Opel wurde auch Fiat mit diesen Metall-Katalysatoren versorgt.
Auch diese Kemira-Metall-Kats wiesen eine mäßige Dauerhaltbarkeit auf. Vor allem der Trend zu den motornah angeordneten Katalysatoren sorgten dafür, dass die Erstausrüster (OEM) auf die Metall-Katalysatoren von Kemira verzichteten. Aktuell fertigt das Kemira-Nachfolgeunternehmen EcoCat Metall-Katalysatoren für gasbetriebene Verbrennungsmotoren sowie Metall-Katalysatoren und Metall- aber auch Keramik-Partikelfilter für Diesel-Fahrzeuge.
Seit 1985 stellt die Firma Oberland Mangold in Südbayern Metallträger für Abgaskatalysatoren zur Abgasreinigung her. Seit Beginn allerdings fast ausschließlich im Bereich Austausch- und Nachrüstkatalysatorsysteme. Später kamen dann Rußpartikelfiltersysteme (Metall-Partikelfilter) und Mini-Kats aus Metall hinzu. Seit der Gründung konnte sich das Unternehmen auf dem Markt der Katalysatoren erfolgreich platzieren.
Bei der Siemenstochter Interatom in Bensberg beschäftigte man sich im Rahmen der Reaktortechnik häufig mit der Verbindung exotischer Werkstoffe. Das Grundpatent für das Fügen von Metallen mit keramischer Oberfläche, das später auch die Beherrschung der Fertigung von Metallträgern erlauben sollte, wurde von Interatom bereits im Jahr 1978 angemeldet. Das war auch der Grund, warum sich die Degussa zu dieser Zeit an Interatom um Hilfe wandte.
Die erste Anwendung des Interatom-Hartlötverfahrens erfolgte jedoch weder bei Degussa noch Interatom, sondern beim Stuttgarter Kühlerspezialisten Behr. Durch die räumliche Nähe zu Mercedes-Benz hatte sich Behr zur Fertigung von spiralförmig gewickelten Metallträgern entschlossen, die Mercedes-Benz als motornahe Startkatalysatoren verwenden wollte.
Die Vorteile eines motornahen Startkatalysators hatten die Mercedes-Ingenieure Dr. Jörg Abthoff und Dieter Schuster im Jahr 1984 veröffentlicht. Zunächst wurden für die geregelten Startkatalysatoren Keramikmonolithe verwendet. Da diese allerdings nicht die hohen thermischen und mechanischen Belastungen direkt am Auspuffkrümmer vertrugen, mussten sie motorfern eingebaut werden. Durch den langen Weg zwischen den Auslassventilen und dem Startkatalysator sowie dem daran anschließenden Hauptkatalysator kühlte das Abgas zu stark ab und die Katalysatoren sprangen viel zu spät an. Die Folge davon war, dass die Abgase direkt nach dem Kaltstart einen zu hohen Anteil an Schadstoffen enthielten, denn sie passierten den Katalysator ohne Umwandlung. Mit dieser ersten Lösung waren die zukünftigen, verschärften Abgasgrenzwerte vor allem in Japan und in den USA demnach nicht einzuhalten. Aus diesem Grund setzte man bei Mercedes-Benz deshalb motornahe Startkatalysatoren auf Metallträgerbasis von Behr ein, welche den hohen thermischen und mechanischen Belastungen widerstanden.
Für Behr von Vorteil war, dass die Startkatalysatoren nur kleine Durchmesser haben mussten, bei der die einfache Spiralwicklung der Folien sich noch nicht als Nachteil erwies. Sie trugen den Markennamen „Metalit“ und wurden mit teils sehr guten Ergebnissen in Japan und den USA eingeführt. Die Nachteile der simplen Spiralwicklung stellten sich erst später heraus, als das Unternehmen Behr auf Kundenwunsch hin Metallträger mit größerem Durchmesser anfertigte.
Als um das Jahr 1980 die politische Abwendung von der Kernenergie sichtbar wurde, begannen Interatom-Manager nach anderen Aufgaben zu suchen, mit denen man die eigenen Naturwissenschaftler, Ingenieure und hochspezialisierten Techniker weiterhin beschäftigen konnte. Neben den Mitarbeitern standen einzigartige Berechnungs- und Analyseverfahren, Bearbeitungsmethoden und metallurgische Kenntnisse zur Verfügung, die weit über das übliche Industrieniveau herausragten.
Bei Interatom war 1984 eine Abteilung „Neue Technologien“ gegründet worden, die von Dr. Rolf Kottmann geleitet wurde. Innerhalb dieses Oberbegriffs war die Abteilung „Automobilindustrie“ entstanden. Sie sollte neue Produkte entwickeln und die Vermarktung von Interatom-Technologien übernehmen. Im selben Jahr setzte Kottmann den etwa gleichaltrigen Wolfgang Maus als Leiter dieser Abteilung „Neue Technologien“ ein. Wolfgang Maus war bis dato in Forschungs- und Entwicklungsarbeiten für Komponenten des Hochtemperaturreaktors eingebunden gewesen. In der neugegründeten Abteilung sollte Wolfgang Maus zukünftige Produkte entwickeln sowie Service und Leistungen für die Automobilindustrie aus dem Bereich der Nuklearindustrie vermarkten. Interatom hoffte, auf diesem Weg das Aus im Bereich der Kernenergietechnik zu überstehen und das umfangreiche Wissen seiner Mitarbeiter damit retten zu können.
Neben der hohlen Nockenwelle wurde als zweite weitreichende Idee der Metallträger für Autokatalysatoren ins Auge gefasst, an dem schon so viele Ingenieure scheiterten. Außerdem gab es damals die Idee der gasdynamischen Lager (Luftlager) für Abgasturbolader. Dazu wurde eine erste Simulationssoftware für Verbrennungsberechnungen erstellt, die von nuklearen Sicherheitsanalyse-Programmen abgeleitet war.
Um das Metallträgerprojekt fortsetzen zu können, begannen die Interatom-Ingenieure bei der Automobilindustrie nach Interessenten zu suchen. Nach einer erfolgreichen Präsentation in Japan im Jahr 1984 stießen sie auf großes Interesse einiger anwesenden Mitarbeiter japanischer Automobilhersteller, besonders bei Toyota-Ingenieuren. Als weiterer Glücksfall erwies sich die neue strategische Ausrichtung der Interatom-Muttergesellschaft. Siemens wollte zu dieser Zeit verstärkt in die Automobilindustrie einsteigen und gründete den Bereich „Automobiltechnik“, dem später die VDO eingegliedert wurde und der sich dann zu einem profitablen Geschäftsfeld entwickelte. Aber auch ein Hersteller von Abgasanlagen zeigte Interesse an einem Joint Venture mit Siemens.
Zusammen mit dem Automobilzulieferer Uni Cardan gründete Siemens dann am 11. August 1986 das Joint Venture Emitec. Der Name Emitec entstand aus „Emissionstechnologie“ und steht heute für ein weltweit operierendes Unternehmen, das mit großem Abstand der Marktführer bei der Herstellung von Metallträger-Katalysatoren ist. 2011 konnte Emitec sein 25-jähriges Firmenjubiläum feiern.
Weblinks
- 25 Jahre Metall-Katalysatoren
- Metall-Kat-Patent Joseph Christie Whitney Frazer (Auszug)
- Metall-Kat-Patent "Startkatalysator"
- Metall-Kat-Patent "Startkatalysator"
- Metall-Kat-Patent motornahe Startkatalysatoren von den Mercedes-Ingenieuren Dr. Jörg Abthoff und Dieter Schuster - Jahr 1984
- SAE-Paper: New Developments in Catalytic Converter Technology as Demonstrated by Mercedes-Benz 300 SL and 300 CE
Einzelnachweise
- Biogaskatalysatoren | Emissionsminderungsbonus mit Emission Partner. Abgerufen am 7. Dezember 2017 (deutsch).