Puddelverfahren
Das Puddelverfahren (auch Flammofenfrischen genannt) war ein im 19. Jahrhundert verbreitetes Verfahren zur Umwandlung des im Hochofen hergestellten Roheisens in Schmiedeeisen (dann auch Puddeleisen genannt), später auch zu härtbarem Schmiedestahl. Im Puddelverfahren entstand durch Frischen eine von Schlacketeilchen durchsetzte kohlenstoffarme Luppe, die in mehreren Arbeitsgängen durch Schneiden und Schmieden weiterverarbeitet wurde.[1] Schmiedeeisen wurde schon seit der Antike hergestellt, das Puddelverfahren nutzte dafür jedoch erstmals die günstige Steinkohle statt der wegen der Abholzung immer teureren Holzkohle. Dadurch wurde Schmiedeeisen deutlich günstiger. Das Puddelverfahren gilt daher als Schlüsseltechnologie der Industriellen Revolution, neben der Dampfmaschine, der Spinnmaschine und weiteren Erfindungen.
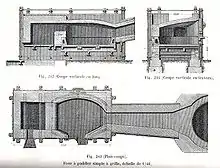
Erfunden hat das Puddelverfahren 1784 der Engländer Henry Cort. Er hatte bemerkt, dass der in heißem Roheisen enthaltene Kohlenstoff verpufft, wenn Luft darüber streift. Während vor dieser Erfindung Kohlenstoff und andere Eisenbegleiter nur durch die von Gebläsen unterstützte Verbrennung von Holzkohle entfernt werden konnten, beruhte sein Verfahren auf der Verbrennung von billiger Steinkohle, ohne dass Gebläse oder Tiegel verwendet werden mussten.
Abgelöst wurde es ab den 1860ern vom Bessemer-Verfahren und dem Siemens-Martin-Verfahren, die erstmals eine Massenproduktion von deutlich günstigerem und reinerem schmiedbaren Eisen ermöglichten, das dann als Stahl bezeichnet wurde.
Terminologie
Gemäß der seit Beginn des 20. Jahrhunderts üblichen Einteilung von Eisen in kohlenstoffreiches, nicht plastisch umformbares, also nicht schmiedbares, Gusseisen und kohlenstoffarmen, umformbaren, schmiedbaren Stahl, wird Schmiedeeisen seitdem unter dem Begriff Stahl eingeordnet. Es ist aber aufgrund einer geringfügig anderen Legierung und insbesondere aufgrund der in ihm enthaltenen Schlackereste nicht identisch mit modernem Stahl.
Früher bezeichnete Stahl nur eine kleine Gruppe von Spezialprodukten mit einem Kohlenstoffgehalt von 0,4 % bis 1,2 %, die schmied- und schweißbar und vor allem härtbar waren. Alle anderen Produkte aus gefrischtem Roheisen wurden als schmiedbares Eisen, Schmiedeeisen oder Frischeisen bezeichnet. Als sich das Bessemer-Verfahren verbreitete, mit dem Flußeisen erzeugt wurde, bezeichnete man schmiedbares Eisen als Schweißeisen und die daraus erzeugten Stähle als Schweißstahl.
Der Name Puddelverfahren, englisch puddling, ist von puddle abgeleitet, was als Substantiv im Englischen „Pfütze, Teich“ und als Verb unter anderem „im Schlamm wälzen / patschen“ bedeutet.[2] Im Töpferhandwerk wird mit dem Verb to puddle die Aufbereitung des Tons vor der Verarbeitung bezeichnet. In der Bedeutung „Pfütze“ bezieht sich puddle auf die zähflüssige Konsistenz des in einem flachen Trog befindlichen geschmolzenen Eisens. Diese Masse musste mit Stangen ständig umgerührt werden. „Umrühren“ heißt im Englischen to stir und ist nicht die ursprüngliche Bedeutung von to puddle. Nach dieser Methode wurde aber nicht nur das gesamte Verfahren der Stahlerzeugung puddling genannt, sondern auch das „Umrühren des Eisens“ zu einer weiteren Bedeutung des Verbs to puddle.[3]
Puddelofen
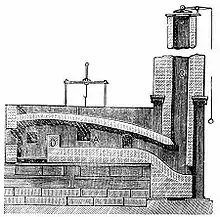
Der aus feuerfesten Ziegeln gemauerte Puddelofen hatte einen gesonderten Verbrennungsraum, in dem Steinkohle auf einem Rost verbrannte. Durch entsprechende Klappen konnte Kohle eingebracht und die Asche entfernt werden. Die heißen Verbrennungsgase zogen unter einer gewölbten Decke durch den benachbarten Arbeitsraum und erst anschließend in den Kamin. Eine kleine Mauer, die sogenannte Feuerbrücke, zwischen Verbrennungs- und Arbeitsraum verhinderte einen Kontakt zwischen Kohle und Eisen. Die Verbrennungshitze wurde auch durch die Ofendecke in den Arbeitsraum reflektiert. Im Arbeitsraum lag das zu bearbeitende Eisen in einer flachen Mulde, die gerade so groß war, dass der Puddler mit seinen langen Stangen noch jeden Teil der Mulde erreichen konnte. Die Mulde war, wie in den Gießereien üblich, mit Sand ausgekleidet. Der Arbeitsraum hatte eine Klappe, durch die die Roheisen-Barren eingebracht und am Ende des Verfahrens die Luppen entnommen wurden, die aber sonst bis auf eine kleine Öffnung verschlossen blieb, durch die der Puddler seine Arbeitsstangen stecken und das Eisen bearbeiten konnte. Auch diese Öffnung konnte verschlossen werden. Die Zufuhr von Luft in den Arbeitsraum sollte möglichst vermieden werden, weil sie das Eisen oxidiert hätte. Eine Klappe auf dem Kamin diente der Temperaturregelung.
Das Prinzip des Puddelofens blieb unverändert. Kleinere Änderungen dienten in erster Linie dazu, die Kosten des Baus und der Wartung der Öfen zu senken. Ursprünglich musste die Sandauskleidung und ein Teil des Mauerwerks wöchentlich erneuert werden. So wurden Hohlräume für eine Luftkühlung in die Feuerbrücke und unter den Arbeitsraum eingefügt oder der Puddelofen durch äußere Gusseisenplatten verstärkt. Es gab Puddelöfen mit einer Art gusseisernem Skelettbau, in das die feuerbeständigen Mauerteile eingefügt wurden. Der Boden unter dem Sandbett der Mulde wurde als gusseiserne Platte ausgeführt. Anstelle des Sandbetts wurde manchmal eine Auskleidung aus Schlacke verwendet. Häufig wurde gegenüber der Feuerbrücke eine sogenannte Fuchsbrücke eingebaut, ebenfalls ein Mäuerchen, das das Abfließen von Schlacke zusammen mit dem Eisen verhinderte. Später wurden die Proportionen an andere Brennstoffe oder Eisenqualitäten angepasst.
Der Puddelofen konnte nicht vergrößert werden, da seine Mulde durch die Reichweite der Arbeitsstangen des Puddlers – und seine physische Leistungsfähigkeit – begrenzt war. Gelegentlich gebaute Doppelöfen waren deshalb eigentlich nur zwei aneinandergebaute Öfen. Versuche mit mechanischen Puddelvorrichtungen waren nicht erfolgreich.
Verfahren
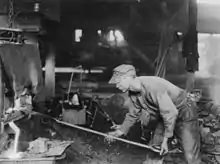
Im Puddelofen wurde eine ausreichende Hitze erzeugt, um das meist als Barren eingebrachte Roheisen zu schmelzen und es anschließend zu frischen, d. h. in einem Oxidationsprozess seinen Gehalt an Kohlenstoff und an Eisenbegleitern wie Silizium, Mangan, Phosphor und Schwefel zu senken. Während das flüssige Eisen sich allmählich entkohlte, stieg sein vom Kohlenstoffgehalt abhängiger Schmelzpunkt. Während die Temperatur im Ofen weitgehend gleich blieb, wurde das Metall immer steifer, bis es zu Luppen zusammengeschoben und dem Ofen entnommen werden konnte.
In der Feuerkammer wurde die in England reichlich vorhandene und deshalb billige Steinkohle verbrannt, während der Arbeitsraum so weit wie möglich luftdicht verschlossen war. Dadurch schmolzen die in der Mulde des Arbeitsraums liegenden 200 bis 250 kg Roheisen-Barren. Die Feuerbrücke verhinderte, dass das Eisen unerwünschte Bestandteile der Kohle wie vor allem Schwefel aufnahm, der es unbrauchbar gemacht hätte.
Der für die Oxidation erforderliche Sauerstoff kam hauptsächlich aus der an Eisen-Sauerstoffverbindungen und anderen Oxiden reichhaltigen Schlacke, die vom Puddler ständig mit dem zähflüssigen bis teigigen Eisen in Kontakt gebracht werden musste. Der Puddler musste dazu das Roheisen mit der auf ihm schwimmenden Schlacke ständig mit seinen langen Rühr- und Kratzstangen umrühren, um den Kohlenstoff und die Eisenbegleiter zu verbrennen (zu oxidieren). Bläuliche Flammen (CO) zeigten den Vorgang an. Der Puddler musste dabei seine Stangen öfters wechseln, bevor sie weich wurden. Infolge des Kohlenstoffverlusts bildeten sich Klumpen von Eisen, die der Puddler in 4 bis 6 gleich große, etwa 40 kg schwere Haufen zusammendrückte, aus denen sich blumenkohlförmige Luppen bildeten. Bei unzureichender Bearbeitung konnten die Luppen auch auseinanderfallen, so dass sie der im Akkord arbeitende Puddler erneut bearbeiten musste. Die Luppen wurden zur Feuerbrücke geschoben, dem heißesten Ort in der Mulde, wo sie bei geschlossener Arbeitsöffnung für 4 bis 6 Minuten der größtmöglichen Hitze ausgesetzt wurden.
Anschließend wurde die Klappe des Arbeitsraums geöffnet, die Luppen mit einer Zange entnommen und über den Hallenboden des Hüttenwerks zum wasserbetriebenen Fallhammer, seit der Erfindung von James Nasmyth in den 1840er Jahren auch zum Dampfhammer geschleppt. Später wurden sie in Wägelchen transportiert. Als Letztes ließ der Puddler die flüssige Schlacke aus dem Ofen ablaufen.
Die Menge und die Qualität der erzeugten Luppen hingen im Wesentlichen vom Geschick und der Kraft des Puddlers ab, die er in einem meist 12-stündigen und nicht selten auch 16-stündigen Arbeitstag einsetzen konnte.
Es bildeten sich drei verschiedene Verfahren heraus:
Puddeln auf Sehne | mit maximal 0,3 % Kohlenstoffgehalt; |
Puddeln auf Korn bzw. Feinkorn | mit 0,3 % – 0,6 % Kohlenstoffgehalt; |
Puddeln auf Stahl bzw. härtbares Eisen | mit 1,0 % – 1,3 % Kohlenstoffgehalt. |
Das Puddeln auf Stahl war zwar im Patent von Henry Cort als Möglichkeit beschrieben, aber nach früheren Versuchen in Kärnten erst von Franz Anton Lohage und Gustav Bremme aus Unna in den späten 1840er Jahren zur Produktionsreife gebracht worden. Das Verfahren bestand im Wesentlichen darin, dass die letzte Phase der Entkohlung vermieden wurde und die Luppen schneller gebildet und sofort ausgeschmiedet wurden. Es war stark von der Temperaturführung abhängig und von der Fähigkeit des Puddlers, unter der Schlackenschicht, die das Eisen vor der Oxidation mit der Luft schützte (nur) solange zu rühren, bis der richtige Grad der Entkohlung erreicht war. Damit konnten nur sehr erfahrene Puddler betraut werden. 1853 wurden im rheinisch-westfälischen Bergdistrikt ca. 2600 t Schweißstahl erzeugt, was 40 % der gesamten preußischen Rohstahlproduktion entsprach.
So wie der Ofen blieb auch das Verfahren im Prinzip unverändert. In anderen Ländern wurden später auch andere Brennstoffe eingesetzt wie z. B. Holzkohle, Holz, Braunkohle oder getrockneter Torf, wobei die Abmessungen der Puddelöfen den Eigenschaften der Brennstoffe angepasst werden mussten. Man setzte auch flüssiges Roheisen ein, was aber meist an den Platzproblemen in der Werkshalle scheiterte. Faber du Faur setzte Gichtgas aus dem Hochofen als Brennstoff ein, was aber zur Folge hatte, dass eine Störung in einem der Öfen sich unmittelbar auf den anderen Ofen auswirkte.
Weiterverarbeitung
Die Luppe mit einem Schlackengehalt von bis zu 4 % wurde unter dem Hammer zu porösen Fladen geformt, die von einer Rillenwalze in flache Stäbe gepresst und geschnitten wurden. Mehrere solche Stäbe aus verschiedenen Produktionen mit unterschiedlichen Eisenqualitäten wurden anschließend mit Draht gebündelt, im Schweißofen erhitzt und wiederum zu Stäben gewalzt, bis nach mehreren Arbeitsgängen das fertige Halbzeug in Form von Stangen, Blechen oder Platten entstand. Dabei wurde der Schlackengehalt bis auf 0,6 % verringert, konnte aber nie ganz entfernt werden. Schweißeisen war immer schlackenhaltig, die dadurch entstehende Maserung war am Bruchgefüge mit bloßem Auge erkennbar. Schweißeisen war deshalb korrosionsbeständiger als Flusseisen.
Mit der Verbreitung des Schmiedeeisens entwickelten sich auch die Verarbeitungsverfahren: 1820 erhielt John Birkinshaw ein Patent zur Herstellung gewalzter Eisenbahnschienen, die die Grundlage für den Bau des Eisenbahnnetzes wurden. T-Träger wurden anfänglich aus Winkeleisen und Blechen genietet. 1830 wurden in England die ersten T-Träger gewalzt. 1839 erfand James Nasmyth den Dampfhammer. Die größten und stärksten Bleche, die 1847 für den Bau der Britanniabrücke gewalzt werden konnten, maßen 3,65 m × 0,71 m und waren bis zu 2,44 cm stark.[4] Doppel-T-Träger konnten nach der Erfindung des Universalwalzwerks 1849 als Profil gewalzt werden. 1851 walzte Alfred Krupp erstmals einen nahtlosen Radreifen, für den er 1853 ein Patent erhielt. 1861 nahm er den Dampfhammer „Fritz“ in Betrieb, der ein Hammergewicht von 30 t hatte, das später auf 50 t erhöht wurde.
Verbreitung
Das Puddelverfahren wurde 1784 von Henry Cort entwickelt und verbreitete sich zunächst von Südwales aus in England und Schottland, ab 1820 auch auf dem Kontinent. In Deutschland wurde das Verfahren 1826 von Friedrich Harkort in seinem Werk in Wetter eingeführt. Während der beginnenden Industrialisierung erlangte es zunehmende Bedeutung (z. B. für die Herstellung von Dampfmaschinen und Eisenbahnschienen). Um 1810 sollen mehr als 94 Puddelöfen existiert haben. Zu Beginn der 1860er Jahre gab es 3600 Öfen. Gutehoffnungshütte (GHH) betrieb 1863 im Walzwerk Oberhausen 60 Puddelöfen.[5] Der Höchststand wurde 1873 erreicht mit 7264 Puddelöfen in 287 Eisenwerken. Die im Puddelverfahren produzierte Menge stieg in Großbritannien und Frankreich bis 1882, in Deutschland und Belgien bis 1889. Gleichzeitig ging aber der prozentuale Anteil an der Gesamtproduktion von Eisen und Stahl laufend zurück, da die Gesamtmenge zunächst durch das Bessemerverfahren und wenig später auch durch das Siemens-Martin-Verfahren erhöht wurde.
Das Bessemerverfahren setzte sich anfangs nur langsam durch, da es auf phosphorfreies Eisen angewiesen war, während die Puddelöfen unterschiedliches Eisen zu einer breiten Produktpalette verarbeiten konnten. Die Verdrängung des Puddelverfahrens durch das Bessemerverfahren begann auf dem lukrativen Schienenmarkt, aber das Puddelverfahren wurde noch lange für viele durch Schmieden erzeugte Produkte bevorzugt, so auch von der britischen Marine, die wegen der besseren Korrosionsresistenz auf seiner Verwendung im Schiffbau bestand. Mancher Unternehmer wartete wohl auch auf das Ablaufen der Patente.
Erst als im Laufe der 1880er Jahre das Thomas-Verfahren eingeführt, seine Kinderkrankheiten überwunden und die Produktion unterschiedlicher Stahlqualitäten in großen Mengen beherrscht wurde, setzte die Verdrängung des im Puddelverfahren erzeugten Schmiedeeisens ein. Im Brückenbau wurden die ersten Stahlbrücken erst in den 1890er Jahren errichtet. 1913 war der Anteil des Schmiedeeisens auf wenige Prozent gefallen, nur in Großbritannien betrug er noch 13,6 %. Die Konverter produzierten Stahl wesentlich schneller und kostengünstiger.
Verwendung
Schmiedeeisen aus dem Puddelofen hatte einen breiten Anwendungsbereich. Aus ihm wurden u. a. Stab- und Profileisen, Bleche, Drähte und auch Besteck hergestellt. Zahllose Brücken wurden aus Schmiedeeisen gebaut, wie z. B. die frühere Dombrücke in Köln, die Rheinbrücke Waldshut–Koblenz, die Griethausener Eisenbahnbrücke, das Garabit-Viadukt in Frankreich oder die Ponte Maria Pia und die Ponte Dom Luís I in Porto. Auch das damals höchste Gebäude der Welt, der Eiffelturm, wurde aus Schmiedeeisen gebaut.
Siehe auch
Literatur
- Oscar Stillich; H. Steudel, Eisenhütte. Eine Monographie, R. Voigtländer Verlag in Leipzig [ca. 1908], Seiten 90 bis 100
- Handbuch der Eisenhüttenkunde Band 3 von A. Ledebur, 5. Auflage, Verlag von Arthur Felix, Leipzig 1908, Seite 195 ff.
- Akoš Paulinyi: Das Puddeln: Ein Kapitel aus der Geschichte des Eisens in der industriellen Revolution. (Abhandlungen und Berichte, Deutsches Museum, N.F. Band 4) Oldenbourg, München 1987, ISBN 3-486-26200-9.
- Adolf Ledebur: Der Holzgaspuddelbetrieb zu Zorger-Hütte am Harz. 1860
Weblinks
- Bei den Sklaven der «Alpinen» – Eine Nacht im Schwechater Werk, Augenzeugenbericht aus dem Jahre 1900 von Max Winter
Einzelnachweise
- Die Angaben in diesem Artikel beruhen im Wesentlichen auf der Schrift von Akoš Paulinyi: Das Puddeln: ein Kapitel aus der Geschichte des Eisens in der industriellen Revolution. Oldenbourg, München 1987, ISBN 3-486-26200-9.
- Puddle. Oxford English Dictionary
- Akoš Paulinyi, 1987, S. 28
- A Resident Assistant: General description of the Britannia and Conway tubular bridges on the Chester & Holyhead Railway. Chapman & Hall, London 1849, S. 16 f. (id=_GsOAAAAYAAJ&printsec=frontcover&hl=de#v=onepage&q&f=false Digitalisat auf Google Books)
- Philipp Stein: 100 Jahre GHH-Brückenbau. Gutehoffnungshütte Oberhausen, Werk Sterkrade, Oberhausen 1951, S. 78.